I had been humming and hawing over purchasing the WE100 for over a year, and on Christmas I finally decided to treat myself. So I ordered the WE100 along with the base, and planned to get some after market higher grit stones. After ordering, I noticed that the after market stones would really only save me 10-15% so I just ordered some higher grit WE stones too. When the WE100 got here, I opened it up and saw that the 600 grit stone had a brutal defect in it.
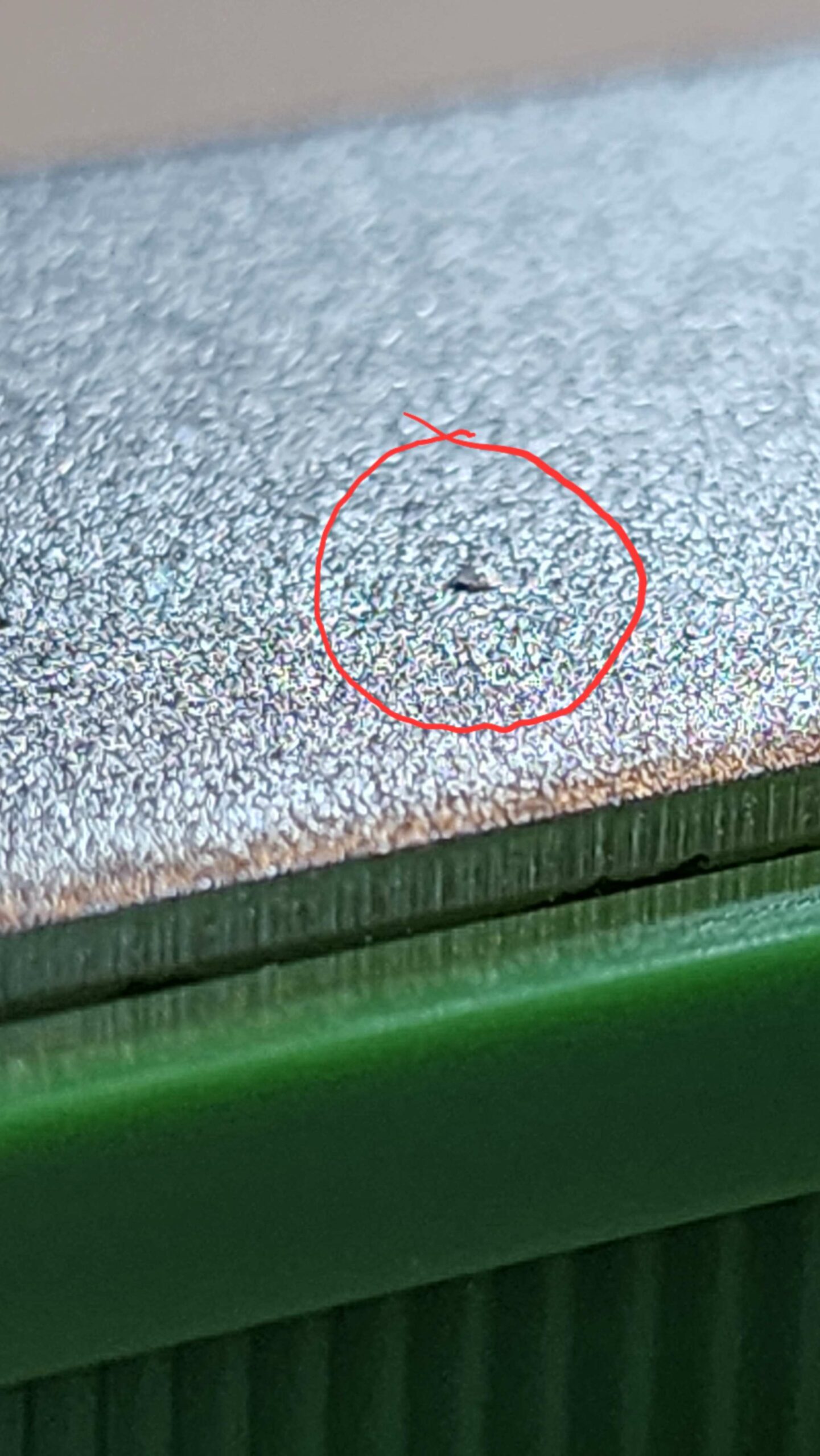
I think it would have taken a chunk out of a knife if I used it.
No big deal really, defects happen. So I messaged the company I bought it through (Thunderbirdgear, I’m up in canada and it looks like they’re the only reseller here), and they said mail the stone back to them, and when they have it then they’ll mail me a replacement.. Kind of annoying but okay. So I’ll maybe get a replacement stone in mid February.
Today, my higher grit stones I ordered arrived.. and before I even opened the package I could see one wasn’t glued to its handle.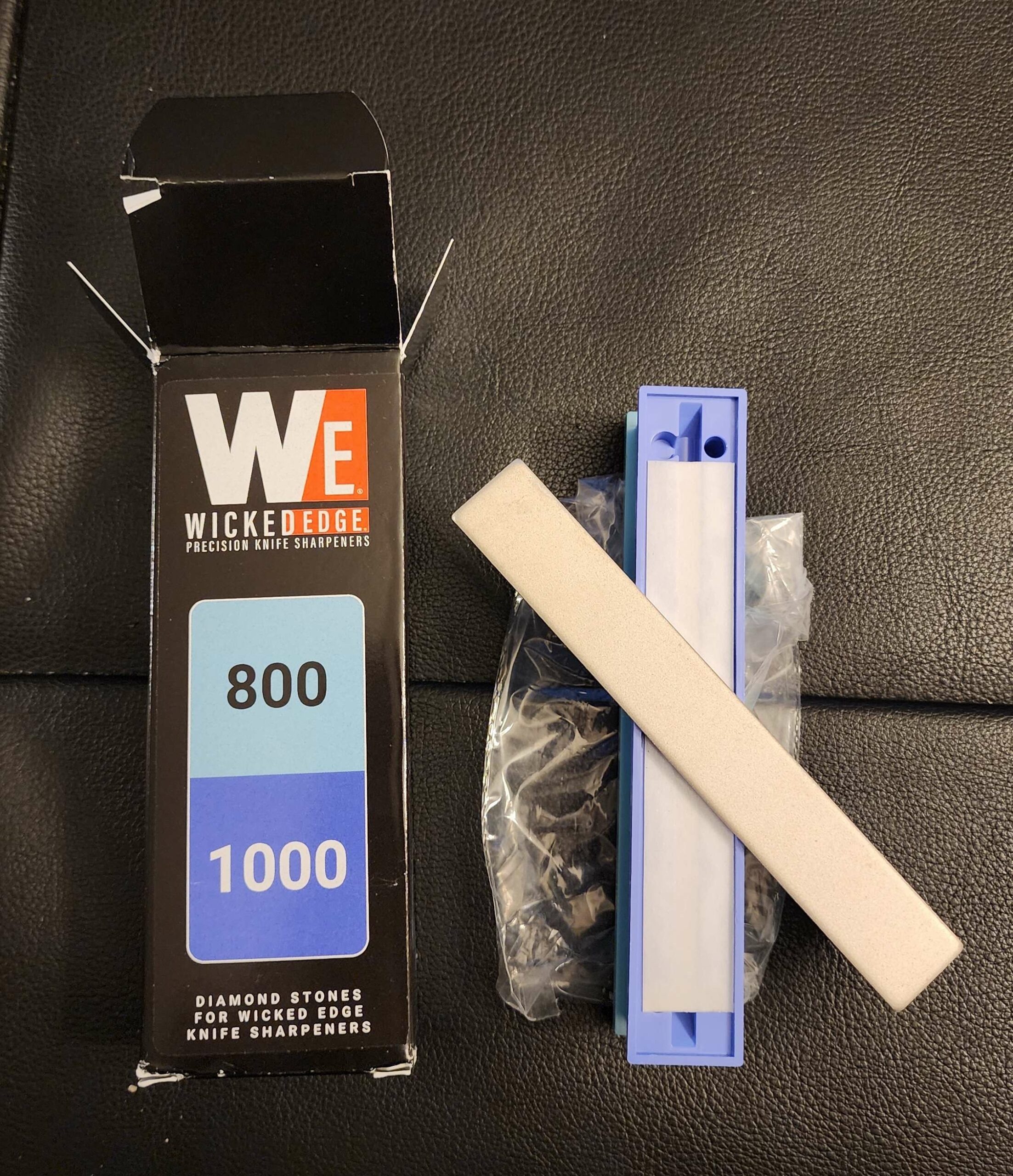
I guess I’ll have to pay another $20 shipping, and wait a month and a half for this one to get back to me too.
Just crazy annoyed after spending almost $700 and finding out its a lemon.
Attachments:
You must be logged in to access attached files.